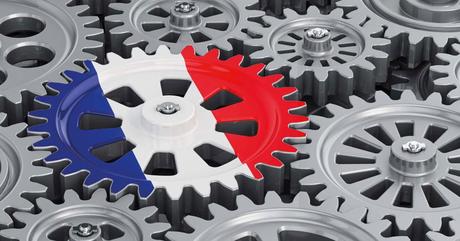
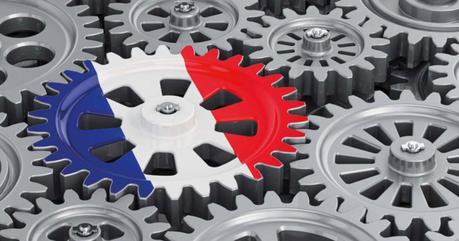
Autres articles
-
51 % des jeunes salariés séduit par l’IA
-
Les actifs risqués tiennent bon
-
La nécessaire adoption des applications finance et achats
-
Le travail hybride : une expression à la mode ou une réalité ?
-
L’ADN synthétique, une révolution à venir pour le stockage de données
La maîtrise du risque
L’un des enjeux majeurs de la relocalisation est de réduire l’exposition de l’entreprise aux risques. Notamment, au risque de rupture d’approvisionnement et de pénurie. Relocaliser la production permet de réduire ce risque.
Le savoir-faire et la qualité
Relocaliser, c’est garder la main sur son savoir-faire. Un point crucial, au cœur des valeurs de l’entreprise. En relocalisant, l’entreprise limite considérablement les problèmes de non-qualité. De plus, elle court beaucoup moins de risques de se faire copier ses produits originaux !
La maîtrise des délais
La délocalisation implique des délais de livraison longs et mal maitrisés. La relocalisation réduit ces délais et permet à l’entreprise de gagner en agilité, tout en évitant les risques de ruptures de stock.
La réduction des coûts
Contrairement aux idées reçues, délocaliser n’est plus forcément synonyme de réduction des coûts. Il y a aujourd’hui beaucoup d’exemples encourageants de relocalisations réussies. Cependant, il faut garder à l’esprit qu’une relocalisation est toujours synonyme de changements majeurs pour l’entreprise. Avec l’arrivée – ou le retour – du volet production, certaines entreprises vont devoir repartir quasiment de zéro ! Les entreprises qui relocalisent doivent passer par une phase d’adaptation, où le fonctionnement global est totalement remis en question. Progressive, cette phase plus ou moins longue passe par différentes incertitudes, tâtonnements, notamment à propos des capacités de production. Durant cette phase transitoire, l’entreprise reprend la main sur la production et réalise en parallèle des approvisionnements complémentaires pour les produits qu’elle n’est pas encore en mesure de fabriquer.
La supply chain doit par ailleurs se réadapter à des délais et des tailles de lots radicalement différents. Plus besoin désormais de disposer de plusieurs mois de stocks d’avance alors que l’usine relocalisée peut produire en seulement 15 jours, par exemple. En définitive, la réindustrialisation doit nécessairement passer par la conduite de changement. Ce processus permet notamment de réapprendre à l’entreprise le métier de la production et l’aide à changer des habitudes souvent ancrées depuis de nombreuses années. La réorganisation en matière de personnes et d’outils autour de la planification industrielle à long terme demande également de tout repenser de A à Z. Or, c’est un point très critique de la supply chain. Pour que la conduite de ce changement soit totalement réussie, certains piliers fondamentaux doivent être respectés. L’un des challenges majeurs consiste à aligner les fonctions de supply chain et de stratégie, de faire monter en compétences certains collaborateurs au moyen de formations adaptées et de recruter pour la fabrication.
Enfin, il est nécessaire de mettre en place un système collaboratif ou chacun communique et où aussi bien les services commerciaux que financiers interviennent pour ajouter leurs connaissances métier à la planification. Dans ce contexte, une bonne option consiste à opter pour un outil S&OP. La réindustrialisation est un processus ultra stratégique. Attention donc à prendre les bonnes décisions et à s’appuyer sur des processus, outils et dispositifs structurés pour mener à bien son projet et aligner le stratégique à l’opérationnel.
A propos de l'auteur : Nicolas Commare est chez Colibri